From water and steam power being ramped up in the first industrial revolution, to the introduction of electricity, computers, and telecommunications devices in the second and third industrial revolutions, we’ve come a long way to having industry adopt a whole new set of technologies. Ones capable of being largely autonomous with artificial intelligence and machine learning taking hold.
For manufacturers and supply chain, industry 4.0 technologies are far beyond a nice convenience to have, but necessary to assist in managing and optimizing all processes to stay competitive and meet the demands of today’s economy.
Industry 4.0 helps describe the introduction and connection of cyber-physical systems, which monitor physical processes to help make decisions (Electronics Media, 2017). Ultimately geared towards production that is faster, safer, and scalable.
What are Industry 4.0 Technologies?
When we describe industry 4.0 technologies, we’re talking about smart systems that operate and learn similarly to humans, but instead of electrical impulses and chemical signals being transmitted by neurons, they are using artificial intelligence, data analysis, and machine learning. There are many examples of these technologies and we’ll cover a few below.
Cloud Computing
Cloud computing delivers services such as storage, networking, analytics, intelligence, and a few others—through the “the cloud” for flexible and quick implementation, as well as being able to scale and match a business’ needs. Microsoft provides a beginner’s guide to cloud computing that can be found here.
The main driver behind businesses adopting cloud computing is that it is scalable and flexible, so that focus can be directed towards general business operations and not on IT infrastructure that needs maintaining. There are many cloud partners available to work with such as Google Workspace and Microsoft Office 365.
Smart Factories
Smart factories connect the digital with the physical. When factories layer in technologies including artificial intelligence, data analytics, and cloud computing, they’re able to monitor all production processes from the manufacturing of parts, to the supply chain, and even individuals working on the floor. This web of technology then monitors, collects, and analyzes data in order to make decisions for optimization, and even predicts potential problems and addresses them before they’re realized.
According to Statista, smart manufacturing is expected to grow close to 480 billion dollars (US) by 2023. This expected growth is a great indicator of the need for more factories to lean into smart technologies in their production processes, as well as a future where skilled tech workers will be in great demand.
Artificial Intelligence
AI is at the center of any smart factory today, as well as many other tech devices that we all have in our homes like Alexa, Siri, and some of the voice recognition tools we find ourselves using. This technology is at the center of industry 4.0. Using computers to take big data, analyze it, and then make decisions is the simple version of how we can describe it.
AI also encompasses the areas of machine and deep learning, in that the algorithms created to predict and react accordingly are AI software, and attempt to mimic the way a human brain works, though far from matching it’s ability, for now. The impact of AI on industry is a major one. The ability to scale up production models without having to compromise quality is one of the central focuses of using AI in today’s production models. Another important aspect of AI is it’s ability to be incredibly accurate as utilizes deep learning. A great example of this is how the Alexa device in many of our homes gets better and better at detecting what we’re going to ask, before we even ask it.
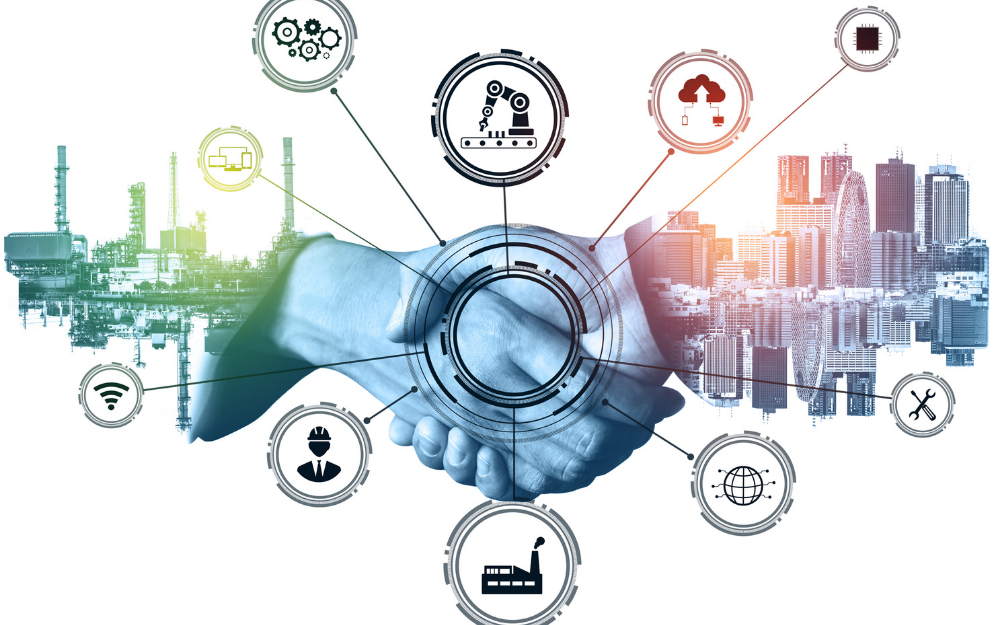
Industry 4.0 Job Outlook
The technology and machinery fueling the fourth industrial revolution isn’t slowing down, and neither are the opportunities for a new crowd of skilled workers in the areas of AI, robotics, digital manufacturing technology, engineering, and others.
According to Samuel Frank, many labor-intensive roles are slowly being replaced by machines that can perform the same operations quicker and safer, ultimately increasing efficiency and capacity in the production process. And though some positions are being phased out, there is an increasing demand for those skilled in being able to design, install, and maintain new technology, as well as operate all of the new machinery.
Because the projected growth rate of traditional manufacturing jobs is expected to decline further, it is important that we train those looking to enter the workforce in these critical technological systems. The University of Michigan-Flint is one of those key institutions at the forefront of bringing our next-generation workers on board with industry 4.0 knowledge and training.
UM-Flint’s College of Innovation & Technology (CIT) offers programs in the areas of:
- Cybersecurity
- Information Technology & Informatics
- Digital Manufacturing Technology,
- Sustainability & Energy Technology
If you have questions or would like to talk more about starting a track into an industry 4.0 career, contact CIT by visiting https://www.umflint.edu/cit/
Contact Dayne Hopkins at [email protected] for inquiries or collaborative opportunities.