The phrase ‘Publish or Perish’ is commonly used by researchers, and their work greatly impacts their evaluations. Stanford University professor John Ionnaidis has worked diligently for years to improve the system used to standardize the evaluation process by looking at how often researchers’ work is used as a reference, cited by other researchers. He has filtered out self-citations and combined several reliable measures of academic impact to make a list of the Top 2% of most-cited researchers in the world. University of Michigan-Flint CIT assistant professor of Mechanical Engineering Khalil Khanafer has made that list.
The current trend in research towards interdisciplinary work is catching up with the way Khanafer has long operated. While Khanafer’s main background is in Mechanical Engineering, his work has overlapped with other disciplines in many ways. In his time working at UM-Ann Arbor, he was an Associate Research Scientist dual appointed with Dr. Ramon Berguer in the UM Frankel Cardiovascular Center and in Biomedical Engineering. “My background is in Mechanical Engineering. Some may say, ‘what are you doing in a Cardiovascular Center?’ He was generating 3D models of Aortic Dissection and Aneurysm from CT Angiograms for numerical and bench-top studies based 3D printing technology to assist in understanding the hemodynamic phenomena that occur within these vascular diseases.
For this, Khanafer’s previous experience with fluid dynamics helped lend insight on the influence of hemodynamic factors on rupture of vascular diseases. His knowledge of testing the materials under various conditions helped to make the models more accurate to what we would find in the human body. “We built aortic dissection and aneurysms from CT scans using 3D printing technology. We would run fluids that mimic the blood through them and experimentally test various conditions.” Khanafer explains. “I take the same model and do some numerical simulations and identify the most common location of rupture.”
Khanafer’s experience applying what he knows to other fields has led to fruitful new directions for his research. For example, he was recently awarded a fund to study the impact of tears size and location on blood flow dynamics in an aortic dissection that builds off his previous experience at UM-Cardiovascular Center and Biomedical Engineering. Khanafer is currently building off research to develop a numerical tool to predict the thermal-mechanical response of the deposited build during the additive manufacturing process. Also, it provides the optimum input parameters for a specific scanning strategy to minimize the Laser-based additive manufacturing’s part quality issues. This leads to a great reduction in time and experimental effort, and also helps to understand the interaction between input parameters and output variables.
Khanafer is conducting experimental work on the thermal and mechanical properties of the 3D printing materials. He is running tests with the help of two Undergraduate Research Opportunity Program interns, Joon Soo Park and Austin Abbasspour to see if printing parts using different scanning strategies offers incremental improvements.
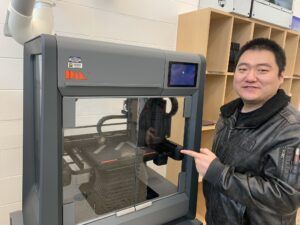
Working in this interdisciplinary space is a big part of why Khanafer’s work has been so off-cited. For the previous work at UM-Ann Arbor, Khanafer says, “We had to pay around $500 each time we would run the printer, and it would, at that time, take up to 50 hours to complete. Any errors cause a waste of both time and money.” This is what got him thinking about improving the 3D printing process. His postdoctoral work at UC Riverside, where he looked at the effect of infusing water with lots of nanoparticles to improve its thermal conductivity, has been widely cited and has got him thinking about other pressing problems in the automotive industry. Khanafer is also partnering with a 3D printing company, Laser Marking Technologies, on his current projects, which is helping them to make immediate improvements in their processes.
Park says of the internship experience, “It is awesome! Having done some of my lab classes online because of COVID early on, the lab experience I’m gaining in this research experience is a really big help.” Park is helping to run the tests on tensile strength, toughness, and hardness of the samples they are printing. Abbasspour is running tests on measuring the thermal conductivity of various materials printed using 3D printing technology.
When asked about the future, Khanafer is full of hope. “People here, they appreciate what you are doing. I feel very supported here, and it feels like a family. And the students here, I’m very proud of them – hard workers and very respectful. I love this environment.”