UM-Flint’s 2016 Engineering Design Day
Each year, graduating UM-Flint Engineering students design, fabricate, and present Senior Design Projects as a culmination of all they have learned. This year they were able to present their work to the campus during Engineering Design Day and also to their Industrial Advisory Board later the same week.
To decide on projects, each student in the capstone course presents an idea relevant to their personal interests and skills. The class votes and the winning ideas are adopted as final projects. The students break into teams based on project choice.
The projects can be inspired by academic competitions, improvements to existing industry equipment, and social or community needs. Two of this year’s projects were responses to needs or issues at the students’ jobs.
With the projects, the students gain experience in working with clients, staying on budget and schedule, and managing both test results and expectations—all in addition to demonstrating their considerable knowledge of engineering practices and equipment use.
Dean Susan Gano-Phillips of the College of Arts & Sciences attended Engineering Design Day and spoke with students from each of the project teams. She noted, “Engineering Design projects are the culmination of students’ experience in the Engineering Program. It is exciting to see the innovative and creative ideas of our students brought to fruition in these collaborative projects.” Gano-Phillips was impressed to learn that all of the graduating students who were ready to enter the workforce already had jobs lined up.
Following are the 2016 Senior Design Projects:
Gear Test Fixture
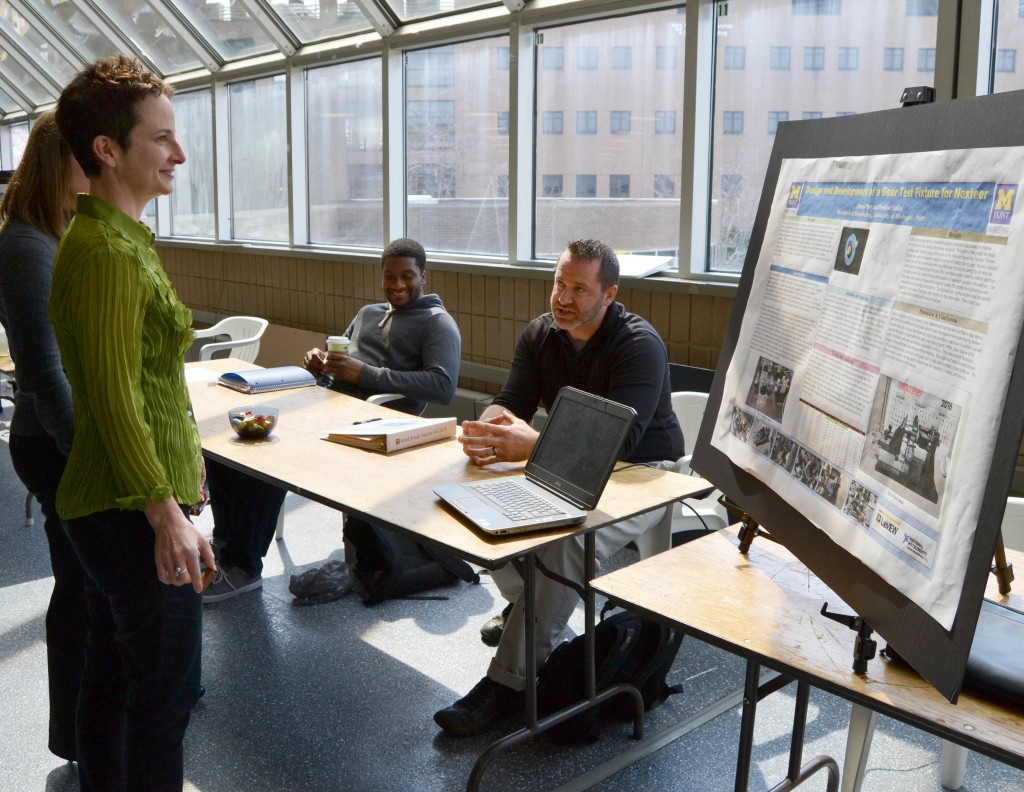
Students: James Pung and Brendon Stokes
This project was directly related to student work at Nexteer Automotive. Much of the product development was done on site in Saginaw, MI.
According to the students’ abstract, “The scope of this project is to develop a gear test fixture that will test strength of a weld joint to attach a worm gear to a drive shaft. The worm gear and shaft assembly are used to drive an electric power steering system at Nexteer Automotive. The fixture must be capable of evaluating the reliability and strength of the weld joint to avoid failure. The fixture was designed to apply load on the gear assembled on the shaft. In the event of weld failure with an applied load, the load will decrease and the gear will stop rotating. The applied load and displacement of the gear will be recorded throughout the test in order to compare the load and number of cycles at which failure occurred.”
They concluded that the “new test fixture was able to perform the test efficiently and was able to meet the requirement specified by Nexteer Automotive.”
Portable Water Filtration System
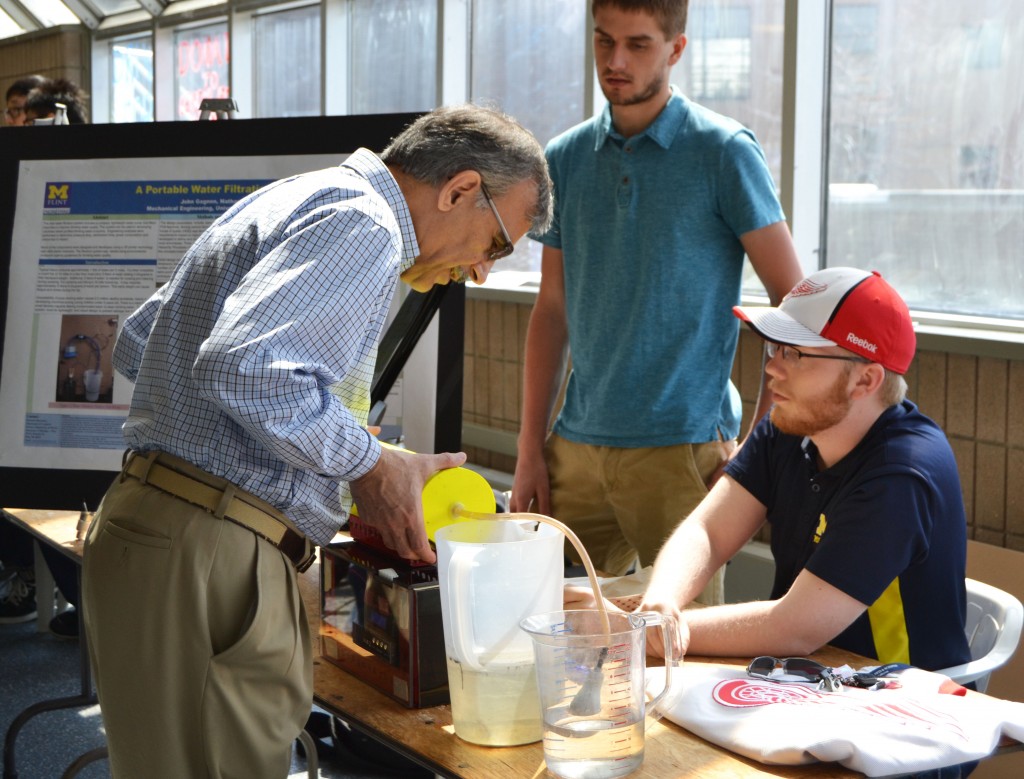
Students: John Gagnon and Nathan Calvert
This group set out to create a water filtration system that was suitable for a wide variety of users, from hikers trying to lighten their loads to children in developing countries who need clean water. The group considered “ease of use, weight, size, rate of flow, capacity, and FDA approval” in their design decisions.
The group notes, “Engineering analyses were performed to determine pressure drop, sterilization time, power consumption, and stress due to impact. Most of the components were designed and developed using a 3D printer technology with ABS plastic materials. The filtration system was tested using environmental protection agency guidelines for drinking water quality.”
To meet all of the standards proposed, the project underwent several adjustments during the design process, including material changes, choosing a different pump, and overall design modifications.
Human-Powered Vehicle (HPV)

Students: Xingyu Chen, Aleah Pavlicek, Terence Staples, and Brandon Walker
This project was inspired by the Human Powered Vehicle Challenge, an annual competition held by the the American Society of Mechanical Engineering. The competition challenges students to think of new ways to provide feasible transpiration options to rural, underserved, or developing populations.
The UM-Flint students considered maneuverability, stability, load-bearing and cargo space, and speed/stopping in their design choices.
Five Speed Manual Transmission System
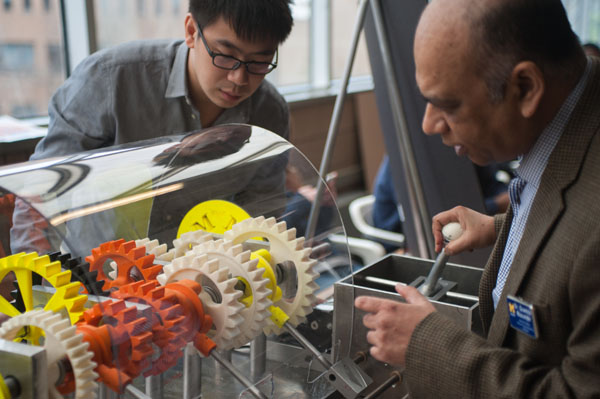
Students: Kenneth O’Brien, Liwei Zhao, and Yang Zhou
Per this group, “The objective of this project was to design, develop, manufacture and test a five-speed transmission system that could be used for teaching and modeling in engineering classrooms. The gearbox was designed with several clear plastic viewing panels to observe the operation of the system. Furthermore, the components were designed for visual demonstration while running at lower speeds. Finally, a flywheel was added to the gearbox to measure rotational speeds. Most of the gearbox components were designed and manufactured using a 3D printer and computer aided design software. Material properties were verified using a tensile tester, the prototype assembly that was tested has met design specifications and required performances.”
This educational model will “demonstrate features, such as shaft, gear, keyed shafts, bearing, and the interaction of different components in the transmission system. Students will be able to measure the input power, input speed and output speed by using speed sensors or tachometers. The transmission model will also aid classroom labs, as students will be able to make predictions and test maximum speeds of the output shaft.”
The group declared the project a success and a “great learning experience.”
Inspection and Rescue Robot
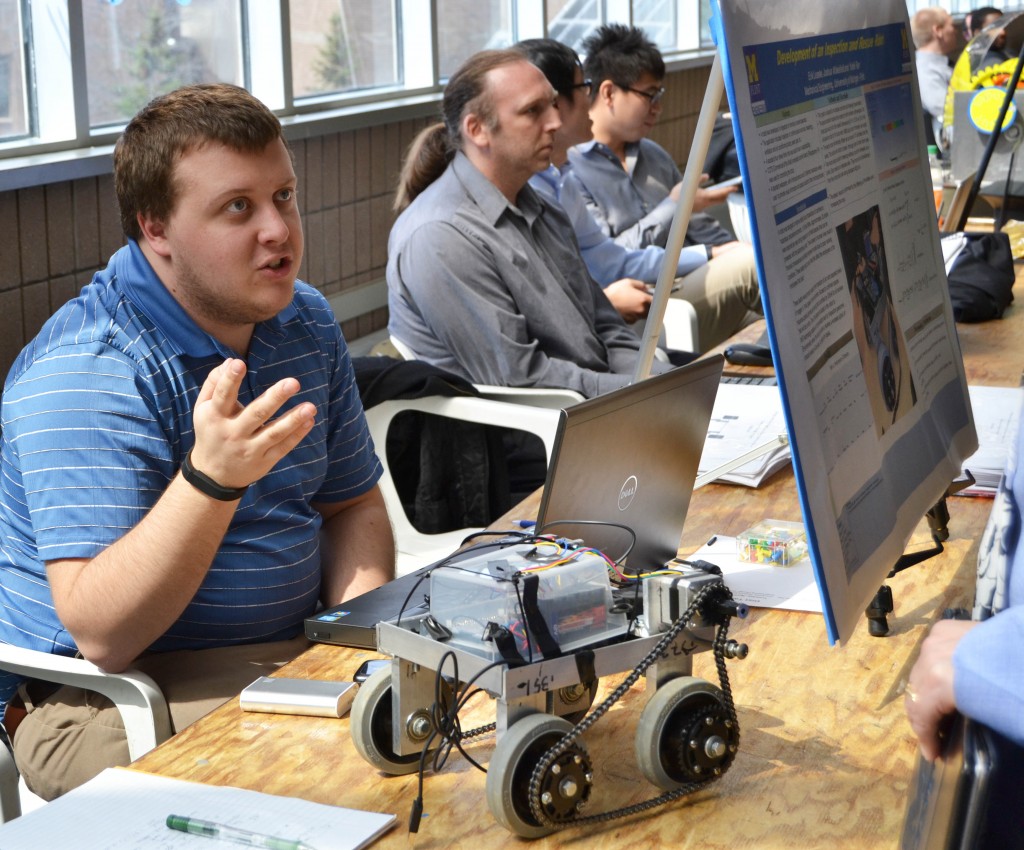
Students: Erik Leaske, Joshua Wakefield, and Yufei Fan
Students in this group wanted to address the number of employee deaths each year that result from the need to inspect confined or hazardous spaces. Their answer came in the form of a small robot that could traverse pipes and other closed environments like heating or ventilation ducts and sewer pipes.
The robot was built on an aluminum frame with consideration given to protecting the camera and electrical components in places that may be wet. The group explored both Wi-Fi and autonomous capabilities as they tried to prepare for the wide variety of uses for their project. Although future improvements could include a plastic frame, “the robot was successfully tested for mechanical performance and design criterion.”
Tugger Cart for Powder Coating Process

Students: Dan Larson, Zach Stevenson, and Sandeep Solanki
According to this group, “There are many hazards associated with the industrial powder coating process. Powder coating operations require the use of curing ovens at high temperatures. The high temperature environment exposes employees to many hazardous situations when they remove carts from the oven. The objective of the project was to develop a system to eliminate the need for an employee to enter the oven. The previous system wasted large amounts of energy due to repeated heating and cooling of the oven to allow employees to enter the oven. A remotely controlled tugger cart would eliminate the need for cool down resulting in an increase in productivity while reducing employee risk. The cart was designed to travel under the racks to move the rack out of the oven. Critical performance requirements included safety, reliability, ease of operation and long battery life. The cart design used a modular concept that is versatile for use in different applications. Additional tests were required to test for the robustness of radio communication to ensure reliability. The proposed cart also had to be cost effective compared to similar systems available in the market.”
As with other projects, this one answered a real-world issue at a student’s employer and also has the potential to greatly increase safety for workers.
For more information on the UM-Flint Engineering, visit umflint.edu/engineering.